It started last year when we were asked to survey a new power plant building to determine if a DAS system was going to be needed. This new building was a giant battery system that would store energy that was produced at nighttime when the demand was low and make it available during the daytime when demand was significantly higher. At the time of the survey, there were many portions of the building that were incomplete and none of the battery systems were installed in the massive football field size building. Our survey indicated that the new building at the power plant was just barely passing, but when the building was complete and the battery systems were installed, we expected that the building would fail.
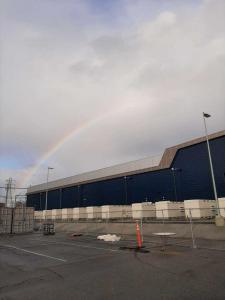
Time went on while the building was continuing to be finished. Again we went out to survey the building and determined that our original prediction was correct. As the building shell was far closer to completion and many of the battery systems were installed, the signal levels fell further and now the building definitely needed remediation work to make the Long Beach Fire Department happy. As a result, we were asked to provide a bid for performing the remedial work of installing a DAS system. We provided them with a bid for the work and waited for about 3-4 months for them to decide to move forward with the project. Unfortunately, at the time they decided to move forward, they informed us that the building was to be on line by the end of December and that they could not get their TCO (Temporary Certificate of Occupancy) without the DAS system being operational. They did not realize how custom their DAS system needed to be based upon the stringent requirements from the City of Long Beach which specified 4 separate bands of operation which included 3 VHF channels, multiple UHF channels in 450MHz, multiple UHF channels in 460MHz and multiple 700MHz channels.
We had previously contacted the manufacturer to get a price quote for providing the DAS equipment for another job in Long Beach that never materialized, so we already had a price bid that was about 18 months old. We figured that the price of the equipment has already gone up, so we provided a quote to the customer who was in a hurry by adding 5% to the price of the DAS equipment from the manufacturer. (When we eventually received a factory acknowledgement for the order, the price had increased by over 30% which now made it so that we were selling the equipment for less than we were paying for it.) The customer quickly accepted the bid and started the process to issue a P.O. (Purchase Order) for the work. Being a large company, they had a complicated process which required us to be signed up as a vendor in their payable system. This required many hours of work filling out different screens of information on the computer, researching the answers to questions in their computer system including information about the makeup of our company personnel. This should have given us a clue what to expect during our installation, but we did not make the connection between their vendor system and what we would be put through during the installation process.
The customer wanted to know what would be the delivery time on the equipment. We told them that standard equipment was typically 4-6 weeks and custom equipment (which was this order) was typically 6-8 weeks. Sometimes we have seen as much as 10 weeks when the factory is backed up with orders. They expressed concern about the 10 weeks delivery because it was getting close to the date that they were supposed to be operational. I told them I would see what I could do to rush the equipment, so I contacted the factory and they indicated that it would be the full 10 weeks. They requested that we order the equipment immediately from our vendor and not wait for us to receive a P.O. from them as that process would take at least 2-3 weeks to get through their system, especially since they could not issue us a P.O. without us being a vendor in their computer system which we had to rectify before we could receive a P.O. from them. So we ordered the equipment from our vendor without a P.O. from our customer to shorten the time line of receiving the equipment which would hopefully be on time to meet their deadline. This is risky because it is custom equipment that cannot be returned and we will suffer a substantial “restocking” charge if we have to cancel the order.
We ordered the equipment from our vendor expecting the delivery to be on time. The vendor that we chose was the first manufacturer of this type of equipment and virtually invented the entire business to solve the problem of reception of radio signals inside of buildings and other structures. Since DAS systems were invented, there have been many other manufacturers of this type of equipment that have started producing these systems, but they do not always have as solid and reliable a design as our vendor. These days, you will find these systems in use in places where the public gathers because everyone wants to be able to use their cellular phone while inside a stadium, arena, office building or thousands of other locations that block the radio signal. A similar but different design is used for the fire department radio so that they will operate inside of buildings.
After 3 weeks, we were finally set up as a vendor for the customer and we received a P.O. We looked at the P.O. and it was correctly issued to us for the price that we were quoted. While we were waiting for delivery of the equipment, the factory eventually sent us an order acknowledgement after we received the P.O. from our customer. When we looked at the acknowledgement, the price stood out like a sore thumb. The price on the amplifier equipment has gone up by 30% over the original price we had been quoted 18 months earlier. This meant that we were now selling the DAS amplifiers for less than we were paying for the equipment which did not set well with us. We looked at whether we should contact the customer, but decided that we would absorb the difference in cost ourselves. Being such a large company, they would probably go into a tailspin if we tried to change the price of the job, so we decided not bother the customer and continue with the project.
It was time to start with the permit process with the City of Long Beach. Each DAS system requires a permit from The City which requires a mountain of paperwork. This was going to be our first job in the City of Long Beach under the new regulations, so the paperwork will have to be done from scratch and not copied and edited from a previous job. We sat down with the regulations from The City and read through them carefully. Then we started preparing the DAS plans while reviewing The City requirements word for word while making changes and additions all along. After many hours of work preparing the plans, we sent them to the draftsman who prepares our drawings on top of the building plans and adds the exhibits that The City wants included with the plans such as cut sheets on the different materials and equipment that we are using for construction of the system. After the draftsman finished with the plans, they were returned to us. We then reviewed the draftsman’s plans and issued revisions to correct things that the draftsman got wrong, misinterpreted what we indicated on our drawings, subsequent changes that we felt were needed to be included or items that we forgot to include in our initial submission to the draftsman. After 1-3 rounds back and forth between us and the draftsman, we finally have a working set of plans for submittal to The City. The plans were forwarded to the customer who wanted to submit the plans to The City.
It was clear that the equipment manufacturer was not going to be able to ship the equipment on time for us to get the system working before the deadline for obtaining the TCO. The factory was able to ship the 700MHz portion of the system, but could not ship the UHF or the VHF portions of the system. After discussing the situation with the customer, we asked the factory to do a partial shipment in which we could get the 700MHz equipment on time. So the factory order was changed to do a partial shipment of the 700MHz equipment.
December has arrived and the date for obtaining the TCO so that the facility can go live is quickly approaching. The customer is getting anxious to have the system installed and Raycom is anxious to complete the project. We called the factory to find out when the 700MHz unit shipped so we could figure out when it should arrive. We scheduled the installation for the day after arrival hoping that the equipment would arrive on the expected day. Fortunately, it arrived on time so we called the customer and arranged to show up the two days later to start installation. That is when the customer dropped multiple bombs on us.
The first bomb was the fact that they did not have the conduit installed to the roof and they decided that they were not going to install the conduit. They asked about the 2 hour fire rated cable being used instead of them installing a 2 hour rated conduit. I told them that we could accommodate the request, but the fire rated cable was expensive at a cost of $100 per foot. They argued that they saw it on the internet for $50 per foot. I told them that was my cost for the cable from a different manufacturer (American Firewire) who was not in town and we could not have the product in time to install the system. The cable we could obtain on time was RFS Celwave “Dragonskin” cable which costs us $90 per foot plus the connectors, hangers, heatshrink and cable preparation tool. We needed to make 3 runs of cable to the roof so we considered running 3 cables. This would have cost over $11K for the additional materials, so we decided to use two crossband couplers at a cost of another $2K. The crossband coupler will combine all 3 BDA amplifier systems into one cable and the second one will break out the single cable to the 3 different base station antennas that are pointed at The City donor site at Signal Hill. This design cost only $5K compared to 3 separate runs of cable for $11K, a considerable savings for the customer who does not want to pay either fee because they changed their minds.
The second bomb was the fact that being a large company with thousands of employees, they have a rigid way of doing business. Power plants can be a dangerous place with many safety hazards. However, this was a new facility and was not in operation, but the customer did not care. We were now being required to have all of our personnel attend a safety class and if we refused, we would not be allowed on premises. We were also being told that we have to wear specific safety equipment which included hard hats, safety vests and steel toe shoes. The one hour safety class meeting represented 4 man hours of time that we did not figure into our costs. We did not like it, but we felt that we could live with it, so we showed up at the proper time the next morning to attend their safety meeting. During the meeting, they outlined additional safety procedures which when added up represented the possibility of doubling the amount of time (or more) it would take us to complete the work. This was also not figured into our quote for the job.
The safety equipment that we needed for the job is as follows:
- Hard hat
- Steel toe shoes
- Safety vest
- Safety goggles that cover the entire eye and the sides of the eyes
- No cut safety gloves
- Face mask
We were required to wear the equipment at all times that we were in the building or on the roof of the building. Many of the tasks that we had to perform required extreme dexterity of our fingers such as installing hardware to hold the cables and antennas to the building ceiling or cable tray, attach connectors to cables, install signal taps, attach the cables to the taps and many other tasks. The no cut safety gloves prevented accidental hand cuts and also prevented us from performing the work efficiently. Another thing that would cause us delays is the right for anyone to stop our work. Anyone who was not satisfied with our safety procedures or if what we were doing conflicted with another trade, anyone had the right to stop our work and then we would have to wait until we were told that we could resume our work.
The first thing we had to do is to fill out a Job Safety Analysis (JSA) form for each day we work at the site. It took over 1.5 hours to fill out the first JSA due to not understanding what they wanted and how it was to be filled out. It was returned for corrections to us at least twice before we got it approved. All this time, we had 4 men standing around doing nothing because we were not allowed to start working until we completed this paperwork. So after arriving at the customer’s location at 7AM for class, it was past 9:30AM before we were allowed to start working on the project.
The next thing we had to do was to get our material over to the building. The roadway around the building was not completed and was an obstacle course. We had hundreds of pounds of materials to get to the building so we had to use a dolly to transport the materials and equipment from the parking lot over 100 yards to the entrance to the building that we had to use. This took several trips to get all of our tools and equipment into the building. In addition, every time we realized that we forgot some item or ran into a situation where we needed some item that we had not anticipated, we had a 10-15 minute round trip to the vehicle to get the items we needed.
It was now 10:30AM and we are finally starting to do some work. The ceiling height was about 25 feet, so all of the cable runs needed a scissors lift to install, but we were not allowed to use the scissor lift without the proper safety protocols which included having a safety harness and being strapped to the lift with the harness. We did not have a harness for every one of our people, so we had to select our lift personnel based upon the availability of a harness and the ability of our personnel to fit the harness that was available. The ceiling had cable tray, but there were 88,000 volt lines in the nearby cable tray that were live, so we had to be careful to avoid doing anything that would interfere with those lines. Also, there is always a danger of that high of a voltage arcing over to us while we were working, so we had to observe rigid safety procedures while running our antenna cables around the building and mounting our antennas. Another problem we had was that we were not allowed out of the central aisle of the building because of other trades working on various aspects of the building or equipment housed in the building. Often we were delayed by others being in our way or some safety concern (which was often overstated) about what we were either doing or what we were about to do. We would then have to stop to explain what we were doing before we were allowed to continue our work.
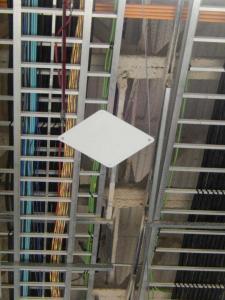
The main task was to run the central cable while installing the signal splitters, taps and antennas, then route the antenna cable into the server room where we were supposed to install the equipment. Nick, Chris and Mark worked on running the cable using two different scissor lifts. The cable that we have to run is a plenum rated ½” hardline cable which is a semi-rigid cable with a minimum of 5” bending radius. While they were working on that part of the project, I went to work trying to get them to install the electrical power, the conduit to the roof and the weather head for the conduit on the roof. All these items were supposed to be installed prior to our arrival at the site and each one of these items could easily prevent us from completing our tasks if they were not ready for us on time.
I then went to work installing the first connector on the Dragonskin cable. This is a new cable that was recently released for sale and we had never had a need for the cable until now. We had to make a special trip to the supply house to pick up the cable, connectors, preparation tool, heat shrink tubing and cable hangers. The directions for the connector installation were written by an idiot and did not properly explain the process since the connector was designed for a different hardline cable, but when the manufacturer developed Dragonskin cable, they did not want to design a new connector just for this cable, so they adapted the existing connector to use with the Dragonskin cable through an unprofessional method. I have installed over 100,000 hardline connectors, so I have a lot of experience with these types of installations. Most hardline connectors take me a few minutes to install, but this connector installation took me over one hour working at the tailgate of my vehicle without having to wear any of the offensive safety equipment that was required inside the building.

As time went on, we managed to get the cable into the server room and routed it down the wall to the location where our equipment was to be located. We installed the connector on the cable even though it was too long because I wanted to test the cable for return losses to verify that the antenna system was sound and performing properly. We then started installation of the Dragonskin cable to the roof. While we were working on that part of the job, another worker drove over our antenna cable with the new connector that I installed with a scissor lift and ruined the cable. Fortunately, the cable was longer than needed and we were able to cut the cable shorter and reinstall the connector.
Our men prepared to go to the roof and mount the antennas. Earlier, I had assembled the antennas and gotten them ready to be hoisted to the roof. Chris and Nick were the two who were going to install the antennas, so they climbed up the ladder to the roof and used their rope to lift the materials up to the roof to install. They tried to mount the antennas to the parapet wall as per the agreement with the customer as to how we were to mount the antennas, but the guys ran into a problem that needed some materials that we did not have to resolve the problem. Therefore, they had to invent a temporary mount to allow us to get the system on the air. We would have to remount the antennas correctly another day. The place where the 700MHz antenna had to be mounted required more cable length than we had on the Dragonskin cable, so we had to come up with a scheme to be able to “stretch” the cable to reach the temporary antenna location, at least on a temporary basis so that we could get the system on the air. We managed to accomplish the task, but as a result, the Dragonskin cable was too short to reach the equipment in the server room. The Dragonskin cable ended about 15’ above the floor, so I had to get outfitted with a safety harness along with all the other safety gear that I was already wearing and attempt to install the connector on the other end of the Dragonskin cable. After working on the connector for about an hour, I finally managed to complete the installation of the connector. I lowered the scissor lift and quickly removed the safety harness and went outside the building where I could take off the rest of the safety gear that was irritating me.
After a brief rest, we proceeded to mount the 700MHz amplifier to the backboard. The power outlet for the equipment had not been completed as it was nothing more than a conduit and a conduit box. There was no wire in the conduit to power anything so now we had to find another way to power the equipment. Most of the power outlets in the rood did not seem to function. I tested several outlets and they were all dead. There was a working outlet about 30 feet away, but it was powering other equipment and we did not feel that we could unplug any of that equipment without causing a problem for someone else. After searching for extension cords and moving equipment in the room, we finally discovered a working outlet that was just in range of the power cord. We plugged in the amplifier and allowed it to boot up. The amplifier was in alarm, so I needed to return to my vehicle and get my laptop computer to find out what was wrong. After the trip to get the computer, I booted up the computer and got it talking to the BDA amplifier. The alarms needed to be disabled until we could complete the installation which took only a few minutes. Now the amplifier was working.
It was 6:30PM and we had been there for 11.5 hours. We were ready to go home and we were confident that the amplifier was working. We packed up our tools and materials and headed to the vehicles. It took 3 trips to the parking lot to get all of our stuff back to the cars. While we were working on clearing out, one of the men from the customer came by and asked if we were done. We indicated that we were finished for the day and were heading home. He wanted to know if the system was working and I said that I felt that it was working properly. He then told m that the fire inspector was coming the next day and that it needed to be working. I said that we were done for the day and we were going home. He insisted that we stay and run extensive tests to verify that it was working. After arguing with him for about 10 minutes, I finally gave in and agreed to run the tests. This required carrying a considerable amount of equipment into the building from the vehicles, running the tests and carrying everything back to the vehicles after we were done. We ran the tests which conclusively indicated that it was working well and that the fire marshal would be pleased with the operation of the radio system. By the time we were finished with the testing, it was 8:30PM. We were all exhausted, but I had to go by the office to get ready for the work the next day. I managed to get home by 10PM that night, just in time to take a shower and pass out without any dinner.
The next day, the fire marshal showed up for his inspection of the building to get the TCO issued which would allow the customer to start operations of the plant. The fire marshal passed the building and issued the TCO. I was half expecting a call from the customer thanking us for our heroic work to get the system operational on a temporary basis, but no call was received. Days and weeks went by and no communication was received from the customer. On the theory that no news is good news, we concluded that the fire marshal issued the TCO. This was confirmed when we called the customer to schedule the next portion of the installation.
Three weeks have passed since we installed the initial system. We have gathered additional materials and resolved many of the issues that we had with the first day of installation by obtaining the specific hardware that we needed to complete the antenna installation. So we scheduled the job with the customer and informed them what day we planned to be there and the time we would be there. I planned to be there at 6:45AM to fill out the JSA and the rest of the crew planned to be there at 7:30AM to start working. I arrived on time and obtained the blank form to fill out. I sat there for 45 minutes working on the form, hoping that I could get the form completed to their satisfaction on the first try. I submitted the form and the person reviewing it found a few mistakes which we went over and then he approved it. This made me very happy as it was now 7:30AM and time to go to work. This time, they had us park in a different parking lot that was about the same distance from the building.
We moved our vehicles to the other parking lot and proceeded to grab our tools and equipment. We proceeded to haul our tools to the server room along with the 3 battery backup systems. Chris and Nick proceeded to go up the ladder to the roof and started to build the permanent antenna structure. They used the rope to lift the antennas as well as the mounting hardware, cable clamps, antennas pipe masts and all other materials that they needed. They proceeded to build the structure and mount the antennas. We worked on getting the antennas properly set on the roof while we pulled the Dragonskin cable off the roof and lowered it into the building where we located the crossband coupler. The plan was to have 3 regular LDF4-50 ½” hardline antenna cables run from the antennas through the weatherhead and into the building so Mark & I rolled out the appropriate amount of hardline cable and installed the connector on one end of the cable. This allowed Nick and Chris to connect the cables to the antennas, seal the connections, route the cables to the weatherhead and drop the cables into the conduit to enter the building. Then Mark had to work on the lift inside the building to install the crossband coupler and terminate all 3 antenna cables with connectors and attach them to the proper ports on the coupler. The other side of the crossband coupler was attached to the Dragonskin cable which allowed us to lower the Dragonskin cable enough so that it would now reach the DAS equipment backboard. The lower end of the Dragonskin would now be connected to another crossband coupler to split the signal by frequency to the 3 different amplifiers that were to be installed. After completing all the small details, it was time to clean up for the day and head home.
Now we were waiting for the two additional amplifiers to be shipped from the factory. We spoke to the factory and they indicated that the amplifiers would be shipped the next week. When next week arrived, the factory indicated that the UHF portion of the system was being shipped that day, but the VHF system still had some issues and the factory was still working on that unit. The next week they were still working on the VHF unit, but eventually resolved the problems and shipped the unit on Wednesday. Since the equipment was arriving from back east, it is normally 5 days in shipping, so we expected to receive the unit Wednesday of the next week. We prepared to go to the customer’s location on Friday after receipt of the equipment so I called the customer and informed them that we would be there at 7:30AM to start installing the balance of the equipment. We received the equipment on time and loaded it into our vehicles on Thursday afternoon to be ready to arrive on Friday morning.
Friday morning arrived and I arrived at 7AM to prepare the JSA and I had it fully approved by 7:30AM when the rest of the crew arrived. We were about to leave the parking lot and enter the building when they informed us that they were completing a 24 hour test and it would be 2 hours before we would be allowed to enter the building. This would have wasted another 8 man hours of time due to their safety protocols and requirements. Fortunately, we had about 1 hours work for Nick and Chris to perform on the roof of the building which was not going to interfere with their test, so we sent them up to the roof to complete the antenna work that they could not complete on the previous trip because we ran out of the special mounting clips needed to secure the cables. Once they were finished with the antenna work, they returned to the parking lot and waited with Mark & I until we were allowed to enter the building after the test was completed.
The first thing we planned to do once we had access to the building was to drive the van to the back of the building and unload the first amplifier so that we could mount the amplifier on the wall. We had asked for additional backboard to be installed because we were going to run out of space to mount the amplifier the day before, but they still has not gotten around to installing the additional backboard. This was preventing us from completing the task, so we had to do everything we could to keep busy while they completed their task. We remounted the 700MHz BDA amplifier to make more room for the other two amplifiers. We then mounted the UHF amplifier which took all four of us since the unit weighed about 200 pounds. We carefully measured the mounting brackets and prepared the anchor bolts to hold the unit while we attempted to mount the unit on the wall. After a considerable amount of work, we had the unit on the wall, but we were unable to mount the third BDA unit because the backboard was still not installed so we turned our attention to installing the battery systems.
The battery system installation had its own unique set of problems including being in the way of installing the last BDA amplifier unit. Since we had 3 systems to install, we started with the battery system for the 700MHz unit which was out of the way of mounting the remaining VHF BDA and the backboard. The battery system is designed in a way that makes it very difficult to install. We had to install wedge anchors in the concrete floor by making a template of the bottom of the battery system. We carefully measured, marked, checked with the template and drilled the concrete. We were able to get the battery system to fit the anchors. While we were working on the battery system mounting, the building people were installing the additional backboard that we needed. Fortunately, the backboard was now completed so we were able to unload the VHF BDA system, transport it inside the building and mount it on the wall. This unit was considerably larger and heavier (about 250 pounds) than the UHF unit which was already big and heavy. Now we had to repeat the same procedure for the second battery system and successfully got it mounted in front of the UHF system. After a lot of blood, sweat and tears mounting the VHF BDA and the second battery system, we then started mounting the last battery system by carefully marking the points to drill the holes in the concrete, installing the anchors and then bolting down the unit. Finally, we have all the large pieces of equipment mounted in place so it is time to wire the units together into a working system.
We started by wiring the AC power to all the devices, but we quickly discovered that we did not have all the parts required to make all the connections. We then started to hook up the 24VDC backup power from the battery systems and found that we did not have the waterproof cord grips to do the job. Most systems that we install come with the cord grips, but this particular manufacturer did not supply the cord grips. The fire department requires them, so we had to source them and bring them back to the jobsite. Since it was now at the end of the day, we decided to go home for the weekend, pick up the parts that we still needed and return to the jobsite next week.
Monday, I had two doctor appointments, so it was decided that Mark & I would use the day to gather the additional materials that we thought that we would need to complete the project. Mark went to pick up the annunciator panel and I went to Home Depot to pick up some electrical supplies. So we headed to the power plant on Tuesday morning and I arrived at the normal 7AM to get a head start on the paperwork. Mark arrived at 7:30AM when I was finishing with filling out the JSA paperwork and proceeded to unload at the building, park our vehicles and went to work on the AC power wiring. I assisted Mark with the power wiring and also worked on the 24VDC wiring to make it more presentable. The grounds had been wired, but it was very haphazard so I wanted to clean up the wiring to make it look professional. The alarm wiring also needed to be done and both the VHF and the UHF systems needed to have the battery system alarms wired over to the BDA so that all of the system alarms were available at the same location. After we proceeded a bit, I had to go to Home Depot on a parts run for additional parts that we had not anticipated. We made a count of the parts that we thought that we needed and picked them up with a few spares. Unfortunately, it became apparent that we needed additional materials that we had not anticipated on the first parts run, so I made another trip to Home Depot to pick up the balance of the parts we needed and also picked up lunch at the same time. I returned to the job site and we both wolfed down lunch and went back to work. We kept going on the project until 4PM at which time we decided to leave and finish the next day.


Wednesday was going to be our day of triumph, figuring that we were going to finish the wiring and hookup, test the system, celebrate and head back to the shop. I finished the ground wiring while Mark was finishing the alarm wiring. It was time to fire up the DAS equipment and test the system. We hauled test equipment into the building and proceeded to run the normal tests to determine how the system was operating. The 700MHz equipment had been operational all along since December, so that totally expected to check out just fine. The UHF system also checked out just fine and the radio coverage inside the building was great. However, when we tested the VHF system, not only did we not have coverage, but we discovered that the factory had built the unit incorrectly by adding an amateur radio frequency. At that point we knew that we were in trouble and that it was not likely that we would be able to recover without sending the VHF unit back to the factory for rework. Additionally, when we measured the system gain, we found that the unit only had +20db gain instead of +60db gain which is a major problem. With both problems, we knew that we were in trouble and that we needed to consult with the factory and review all the original paperwork to determine who made the mistake and how to rectify the mistake. We informed the customer that we had a problem and that we were done for the day. We left the site and returned to the office to have a conference call with the factory in an attempt to figure out what happened, why it happened and what we could do about it.
The phone conference was set up for 2PM at which time we had everyone on the phone. We had looked at the original specification of frequencies that were needed and how it got to where we were currently. From our best ability to tell, the factory man who made the mistake is no longer with the company and the mistake was made two years earlier during the meeting with the Long Beach fire department in January 2019. The mistake carried over to this job by our failing to properly review the order acknowledgement to catch the mistake that the factory made. However, we were able to determine how to correct the defect in the design. We were still speculating what was wrong with the unit that was causing the low gain. We would not know for certain until we returned to the site and ran tests on the equipment.

The next morning was Thursday and we returned to the job site to fill out the JSA paperwork. They were surprised to see us, especially since we showed up without the whole crew to remove the amplifier from the wall. We explained that we had a conference with the factory and had a game plan to figure out how to proceed. We then found out to our extreme pleasure that we did not have to fill out a JSA because we were testing and not installing, so we headed over to the building and proceeded to run multiple tests on the unit. We inspected the BDA and determined how we would perform surgery to remove the extra amateur radio frequency. We had a plan and started the surgery on the input filter. We pulled out the guts of the amplifier system, found the amateur frequency filter, removed the filter and reassembled the guts back into the cabinet. Then we had to repeat the same procedure on the output filter of the amplifier. After we finished, we ran some tests and determined that the operation was a success and the patient had not died! Now we needed to determine why the gain was low. We started taking measurements one state at a time. We measured the power supply to determine that it was not the problem. We found that the power amplifier was the problem. It had failed, so we removed it and was able to easily bypass the bad amplifier. Now the unit was functional in one direction, but still had a problem in the other direction. Again we went through the same procedure and determined that the other direction had the same problem so we removed that other power amplifier and bypassed it to make the unit functional, but at a lower output level. The question was if the lower level would be good enough to get by temporarily. After testing the coverage, the answer was a resounding yes! We had succeeded in making the system functional without sending it back to the factory to resolve the issues we identified. However, we have to send back the defective power amplifiers to the factory to have them repaired or replaced. We were now done for the day. It was about 1:30PM and we packed up and went to check out with the office. They asked if we were done and we said no, because there was still some work that we had to finish. They thought that we should stay and finish. Mark & I both strongly felt that we should come back in the morning and start fresh on the problem with the Dragonskin cable because we did not know how long it would take and we did not want to get part way through the resolution of the problem and have to leave at the end of the day. We insisted that we would be back in the morning in spite of the fact that the customer felt that we were wasting time Thursday afternoon. We had other things to do at the office and knew that it would be a mistake to start on the last problem without sufficient time to finish the task.
Friday was another day and we were at the power plant at 7AM to work on the JSA paperwork which was necessary since we were installing and not testing. So at 7:30AM we headed into the building to drop off our tools, equipment and supplies, then park the vehicles in the parking lot. We returned to the building and prepared for the job of repairing the connector on the Dragonskin cable that had broken off the cable due to attempting to bend the cable into a position that it did not want to do. The Dragonskin is a very stiff cable so it does not bend easily. When you have a tight space, it becomes very difficult to handle the cable which was the case here. Mark grabbed a scissors lift and positioned it outside the server room in the proper place so that I could go up the lift to fix the problem. We had been asked how long it would take at which time I replied that one hour if it cooperated and 2+ hours if it did not cooperate. So I donned the harness that was too small for me and I proceeded to load the tools onto the lift. I then climbed into the lift and proceeded to raise the lift to the ceiling. This was the first time I actually saw how the installation had been done and saw the broken shield on the Dragonskin cable, so I proceeded to remove the connector which is no easy task. These connectors once they are installed, do not remove easily and the location where I was working was poorly lit because I was above the lighting that was pointing down and I was working next to the 88KV power cables that were in the cable tray that was acting as my work table while being 22 feet above the floor. So I worked at removing the connector so that I could fix the problem while trying not to drop any of my tools. I had to take off the safety goggles since I could not see effectively with them and I had to hold my flashlight in my mouth as I worked. Eventually, I managed to get the connector off the cable and brought it down to the floor at which time I took it into the server room and used the power transformer as a table to work on it. It became apparent that the connector was damaged beyond repair and that we would need another connector. (This is the reason we did not want to start later in the afternoon on this problem as we suspected that the repair would not go smoothly.) I immediately got on the phone and ordered another connector from the distributor and Mark went there to get the new connector. This was a one hour round trip to obtain another connector and I kept busy working on other portions of the repair job until Mark returned with the new connector.
Mark returned with the connector when I was finished with everything else with the preparation. Now I had to engage in the process of attaching the new connector and getting it right so that we would not have another problem. It took quite some time for me to get the connector attached properly. There are many steps to prepare the cable starting with cutting the cable with the cable preparation tool. The tool performed well for what it was designed to do, but it did not perform the entire cable preparation. There were 3 layers of material under the cable jacket which was cut by the cable prep tool at the proper location, but the tool does not remove the jacket. That still had to be done manually. There was a layer of fibrous material under the jacket that had to be pealed off and was stuck to the material below. Then there was a layer of thick metallic foil that was part of the heat shield and then another layer of the fibrous material that both needed to be removed. Then the special gasket had to be installed in the proper corrugation of the cable before inserting the connector backnut on the cable. The backnut had to be pushed down to the point where the connector collet could be installed in the last corrugation before the end of the cable and then the backnut needed to be slid forward to capture the collet. I then had to cut the center conductor to the correct length and remove the burrs that could damage the center pin of the connector and scrape the center conductor to remove any film on the conductor so that it makes good contact to the center pin of the connector. Now I had to install the front body of the connector to finish the assembly. It connector looked like it was properly installed and measured OK with the ohmmeter. Now it was time to connect the cable to the crossband coupler but the cable was too short. So I had to lower the lift and Mark had to drive it through the doorway while trying not to be decapitated to the other side where we had to cut some cable ties that were preventing us from being able to pass enough cable to the other side of the wall to reach the crossband coupler. Once we did that, Mark had to drive the lift back to the other side of the wall so that I could finish the job of connecting the cable with the new connector. Once I did that, we performed a quick test on the system to verify that it was working and then we removed the temporary cable that we had installed the previous week to keep the system on the air. However, to do that, Mark had to drive the lift back through the doorway while avoiding decapitation again so that we could cut the cable ties for the temporary cable and completely remove it.

Now it was time to perform a final test on the system for the day to determine if all of the bands were functioning properly. We walked the entire building checking the signal level while we were out and about the building. We were quite pleased with the signal levels so we proceeded to pack up all of our tools and equipment. It was about 12:30PM and we had a 1:00PM meeting at the office. We just had enough time to get back to the office for the meeting and it took 5 hours to fix the broken connector which validated our decision not to attempt the repair of the connector the day before.
At this point in time, the entire system is functional except for the annunciator and the fire alarms which are waiting for a decision to be made as to where to install it. All the difficult work was done and what is left to do is minor work for one person. The job turned out very well and we are proud of the job that we did. After adding up the hours we spent on the job, we spent more than double the amount of time that we originally figured it would take to do the job. When considering the surprise price increase the factory gave us on the equipment, we are still wondering if we have paid the customer for the experience we received, especially since the job has not been billed or collected and we have already paid for almost all of the materials and all the labor.
Now it is time to negotiate with the customer to discuss the cost overruns that were caused by their changes in the plan including the Dragonskin cable, the crossband couplers and all the extra labor due to their safety protocols. Regardless of how it turns out, we felt that it was important for Raycom to provide what was promised in spite of the obstacles that they threw in our path.
Another job well done…………….