A few years back I did an experiment on social media. I was curious about troubleshooting methods that other used. Here is the scenario I posted:
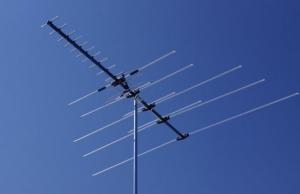
Some people requested more information, as I had anticipated. They inquired about the type of feed line, the presence of amplifiers, and the signal levels at various points. I provided the additional details in response to their questions. The path to the station was unobstructed. The signal strength was approximately 20dBmv for most of the antenna. There was a 20-foot coaxial cable connected to a single TV, and at the TV, the VHF channels still had a signal strength close to 20dBmv (indicating a good signal). However, the UHF channels had a signal strength of around -20dBmv, which is considered poor (as the TV requires a signal strength greater than 0dBmv). This results in a difference of 40dB. The readings were taken using a Wavetek SAM III signal level meter. To provide some clarification, it is important to note that 0dBmv does not indicate no signal; rather, it represents 1 microvolt. The dB scale simplifies calculations by allowing for the addition or subtraction of gains or losses.
There was a lot of speculation:
Improperly installed twinlead- but it was coax. (twinlead is the flat cable that used to be see on older television installs)
External interference- Doesn’t account for the low signal level
Failed UHF amp- A good guess, but there was no amp.
VHF only antenna- Doesn’t match with the antenna signal level readings.
Some individuals attempted to guess the parts that needed to be changed, such as the balun (which converts twinlead to coax), antenna, connections, or coax. While changing enough parts would eventually lead to identifying the correct part (the coax), I found it intriguing that these individuals were content with stopping there and did not investigate the underlying cause of the problem. They were satisfied with simply identifying the faulty part. This approach has been particularly frustrating to me when auto mechanics adopt it. They provide an initial price estimate based on their initial guess, but then call with an increased price after replacing the part and finding that the problem persists. On one occasion, a mechanic made about four incorrect guesses before I decided to take my car back and fix it myself. The problem turned out to be a part that had not crossed his mind because it was not listed as one of the common causes identified by the factory.
Another group of responses were dismissive:
There is nothing interesting on UHF- it was of interest to the customer so the problem needed to be solved.
Get Cable- Rather than fix the problem, just do a work around.
“It’s your fault”- That one was the prize winner. In the original post I had said that it was a thought experiment. I had not done the original install, I repaired it.
One person identified the issue: a cable with a leaking shield due to a manufacturing specification problem. The copper braid shield had inadequate coverage, causing UHF frequencies to escape. Similar to a leaky water pipe, most of the signal failed to reach the intended destination. The responses to the problem were mostly disorganized and lacked structure. Some individuals became upset with me for not simply providing them with the answer. Many did not read the thread where the relevant information was disclosed, instead relying on quick guesses. Certain individuals attempt troubleshooting by memorizing symptoms and solutions, which can lead to confusion when multiple causes result in the same symptom.
Although changing parts can sometimes address the issue, it is not the most reliable approach. This method often leads to the person stopping once the problem appears to be resolved, without investigating the underlying cause. Understanding the reason behind the problem is crucial for preventing its recurrence and for quicker troubleshooting in the future. Relying solely on memorization is inadequate since there is a limit to the amount one can remember, and it fails to prepare for encountering unfamiliar equipment. I once assisted a mystery writer who likened me to one of her detectives. She observed attentively as I checked signal levels and obtained distance readings to identify the fault. Unlike most people who simply wait for the job to be finished, she was thrilled when I successfully pinpointed the issue on my first attempt in another apartment.

Some of the best troubleshooters I knew in the 60s and 70s were the TV repairmen. Of course I am not referring to the do it yourself people that pulled all the vacuum tubes out and took them to Thrifty’s to test. Despite being the object of many comedians jokes they had to understand the circuits they were working on. If a voltage reading didn’t match the schematic, they needed to find out why. Something could be distorting a wave shape, a part supplying power could be compromised. They spent a lot of time sticking test probes in to high voltage circuitry tracking the problem down to an individual part rather than just throwing whole boards away as is done today. Some of us are from that time. We have kept up to date on the new technology but unlike many still have an understanding of the physics beneath it.

When a device is broken, visible signs of the problem are often absent. If a part is visibly burned, it is usually due to an underlying condition that is not immediately apparent. Sometimes, we can quickly identify the problem based on our experience, but there are also instances when it requires more effort. Similar to a detective, we gather clues to form a complete understanding of what cannot be seen. This process begins with obtaining information from the customer, which is not always sufficient. We then examine the device ourselves, looking for any details that may have been overlooked by the customer. Additionally, we utilize test equipment to gather objective data, as subjective observations can lead to incorrect assumptions. Radio problems, for example, are often reported as “static,” but they may actually be caused by intermodulation, power line noise, heterodyne, frequency error, or other factors. Our equipment allows us to measure various parameters such as voltage, current, RF wattage, frequency response, impedance match, modulation, RF signal, return loss, and distance to fault. This provides us with an objective baseline and helps us identify the underlying causes. Using all this information, we form a hypothesis, similar to what we learn in science class. To confirm the hypothesis, we conduct additional tests, which may involve replacing parts or examining the issue from a different perspective. Once the defective part is identified, the next step is to determine why it failed.
We also need to beware of the ways that people, including us can, fool themselves. Cognitive bias can be a factor:
- Anchoring – placing too much weight on the initial pieces of information. Sometimes information gathered later contradicts what was initially provided. It is important to be able to let go of preconceived ideas.
- Bandwagon – “jumping on the bandwagon” What everyone is doing or what everyone believes is not necessarily correct.
- Bias blind spot – the tendency for people to recognize bias on the part of others but failing recognize their own.
- Confirmation bias – People often look for and note information that supports a preconceived idea with dismissing other facts.
- Halo effect – Belief in a person or organization. In technology this may be a noted person, or could be a brand or manufacturer that is noted for it’s size or history. Nobody is infallible.
- Framing effect – People sometimes form conclusions and opinions based on information provided to them with positive or negative connotations. Advertising can often skew perceptions as can the opinions of someone in a company pushing their own opinion.
- Recency effect – the tendency for more recent pieces of information, ideas, or arguments to be remembered more clearly than those that preceded.
Though it may seem like a substantial amount of work, it is an essential part of the job. Learning the system’s functioning and identifying the reasons behind its failure allows for quicker future fixes.
Troubleshooting is not a simple task and requires a systematic approach. Simply changing parts without understanding the root cause of the problem may lead to temporary fixes and recurring issues. It is important to investigate why the problem occurred in order to prevent it from happening again and to improve problem-solving skills for future cases. This also enables us to fix a problem when someone else threw in the towel. Experienced troubleshooters understand the importance of thoroughly examining the evidence, using objective measurements, and considering various biases that may affect their judgment. While this approach may seem like a lot of work, it ultimately allows us to provide more effective and efficient solutions, making it a valuable skill in the ever-evolving world of technology.