By: Mark Abrams
It was a time in 2009 when a fire erupted in the Angeles National Forest. On August 26th, the fire was started by arson in the La Canada Flintridge area and burned 160K+ acres, burned 89 residences plus another 120 other type of structures and killed 2 firefighters. It took almost 2 months to put out the fire from when it started.
Approximately 40 miles of Angeles Crest Highway was damaged from the fire and as a result, the authorities closed off the road as the highway crossed into the Angeles National Forest. This is the route used by everyone to access Mt Lukens for maintenance of the equipment located at the site. However, the authorities had closed Angeles Crest Highway to the public and had severely restricted our access to Mt Lukens. We had to get special permits to access the site, then we were locked out completely. For a while, the authorities only allowed us to access the site 2 times per week in a caravan led by the USFS and only gave us 3-4 hours to repair whatever was broken. At another time, we were completely restricted from going to the site and at other times, we could go there by helicopter. At times, the authorities allowed anyone with a permit to access the site, then the next person on duty had a completely different interpretation of the rules and would not allow anyone except for governmental vehicles. The rules for access to the site for over 18 months changed on a daily (or hourly) basis, making maintenance of the site very difficult.
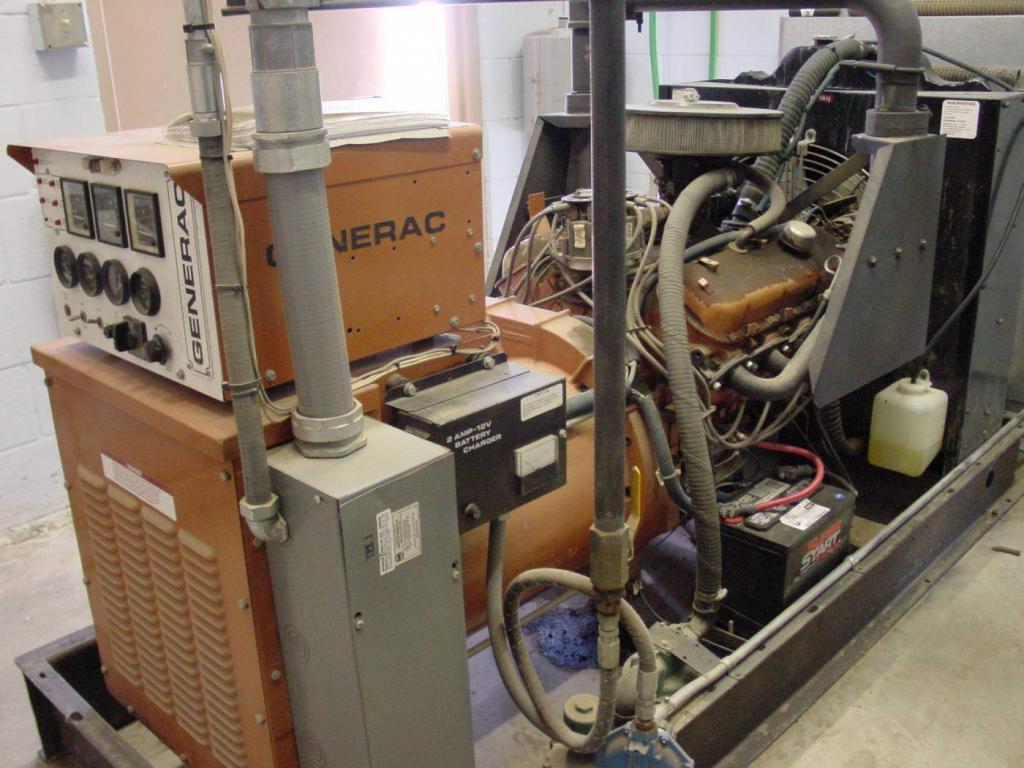
The site was without power from Edison for 12 weeks and it was necessary for all building owners to operate their sites from generators. Some of the building owners did not have a generator and had to rent a generator on a trailer, bring it up to the site and keep it fueled. MRA had a generator permanently installed at our site, but we still had to keep the generator fueled. We have 2 x 1000 gallon propane tanks, but since the generator used approximately 8 gallons of propane per hour, the tanks would power the building for only about 10 days. At that time, we needed to get a propane truck up the hill to refill the tanks at a price of $7000 each time we filled the tanks. We also have battery systems that provide an additional 2 days for only the equipment that was connected to the battery system.
One day, the generator in our building failed in the morning after running for about 8 weeks continuously. One of our personnel got up to the site around 12 noon and found that the belt on the generator had been shredded. He put a new belt on the generator and got it started and running again. He left the site and everything was fine until about 4:00PM when the generator failed again. I then went to the site to check out the generator and found the belt shredded again. There was another belt on site, but after careful inspection of the pulleys that held the belt, I determined that one of the pulleys was broken. The two sides of the pulley were spot welded together and there were stress cracks around the welds, causing the two sides of the pulley to separate allowing the belt to get down into the center of the pulley where the sharp edges of the metal that had fatigued would tear at the belt and finally shred the belt.
There was no way to repair the pulley at the site. The other problem is that the pulley was stuck on the shaft of the governor which keeps the generator running at the correct speed so that we get the correct voltage and frequency out of the generator. Therefore, I had to remove the governor from the generator and take it with me. By the time I got down the mountain, it was 9:00PM, so there was no place that I could go to get the pulley. I went home and made phone calls so that I could get started at 7:00AM the next morning at a machine shop to get the old pulley off the shaft of the governor. After succeeding with that task, I went to Grainger near the LA Airport to obtain another pulley. They did not have the part, but located what I needed at another store. I went to the other store that had a fully cast pulley, one that would not suffer from the same problem that plagued the old pulley. I installed the pulley on the shaft and then headed to the mountain to install the assembly.
When I got to Angeles Crest Highway, there was a different CHP officer guarding the gate and he refused to allow me through the gate to access the site. While I was arguing with him in an attempt to get through the gate, there were two unmarked two government vehicles (with government license plates) that arrived. They were waived through the gate without reviewing their credentials or asking them why they needed access, but he still would not allow me to go through the gate. After about 30 minutes of trying to change the officer’s mind, I left to drive down to where I could get cellular coverage. I called a friend of mine who was a radio technician who worked for the State of California. After explaining the situation, he said to call him back in 30 minutes. I went and had some lunch to occupy the time while I was waiting to call him back. After 30 minutes, I called him and he said that he got through to the right people and that I would have access, but I would have to wait another 30 minutes before everyone was notified. I kept busy for another 30 minutes and then drove back up Angeles Crest Highway to the gate where the CHP officer was located. With no fanfare or delay, the CHP officer opened the gate and let me through. I could see the look on his face that he was not happy since he gotten his hind end reamed.
From that point, it was still another 5 minutes to the US Forest Service Station and 35 minutes up to Mt Lukens on the dirt road. I diligently pursued getting to the site as quickly as possible because we had many customers off the air including LA Unified School District, several taxi companies, paratransit operations for LA County, microwave systems and many other radio systems that occupy space in our building at Mt. Lukens. Our trunking system was still operating on the batteries, but that would not last more than another day or two if I did not get the generator working. When I arrived at the site, the two government vehicles that passed through the gate while I was being denied access were parked in front of our building. It turns out that the vehicles were from LA Unified School District. They had gone to the site to find out why there was no power at the site, but they were standing around unable to do anything to fix the problem. Aside from the fact that their keys did not access the room with the generator, I had the missing part in my possession that needed to be reinstalled on the generator in order to make it functional. They proceeded to tell me that the generator was not running, so I pulled out the governor with the new pulley and showed them that I was already on the problem. I told them that I was the person delayed at the gate when they went through at which time they said that if they knew who I was, they would have told the officer to let me through the gate. I also told them that I needed about 30 minutes to reinstall the governor with the pulley as which time they could expect to be back on the air.
I diligently went to work on the generator while they waited for me to finish. They offered me assistance, but it was a one man job and their help would not have resulted in it getting done any faster. After the 30 minutes were up, I had finished installing the governor and the belt. I got the belt tightened and then fired up the generator. It started right up and continued to run for the balance of the power outage which was another 4 weeks.
As a result of the delays caused by the CHP officer, it delayed me about 2 hours getting the site back up and running with the generator. Many of our customers were inconvenienced including some governmental agencies that rely on our communications infrastructure for their internal communications. This is another shining example of the inefficiencies of government and how they get in the way of solutions instead of facilitating the solution to a problem.
Update: In June of 2021, 12 years later the pulley came loose again. This time the repair was more routine, the trip went without incident, and we gave it a new bolt to hold it in place.