It was 2017 when we bid on a contract with the Freeway Service Patrol (FSP) to provide radio communications service to their fleet of vehicles that provide assistance to stranded motorists. The demands of their service area could not be serviced by one tower site which meant that they had communications issues which could not be solved with a simple radio system.
The one area that they traveled where we did not have good coverage was the Cajon Pass.
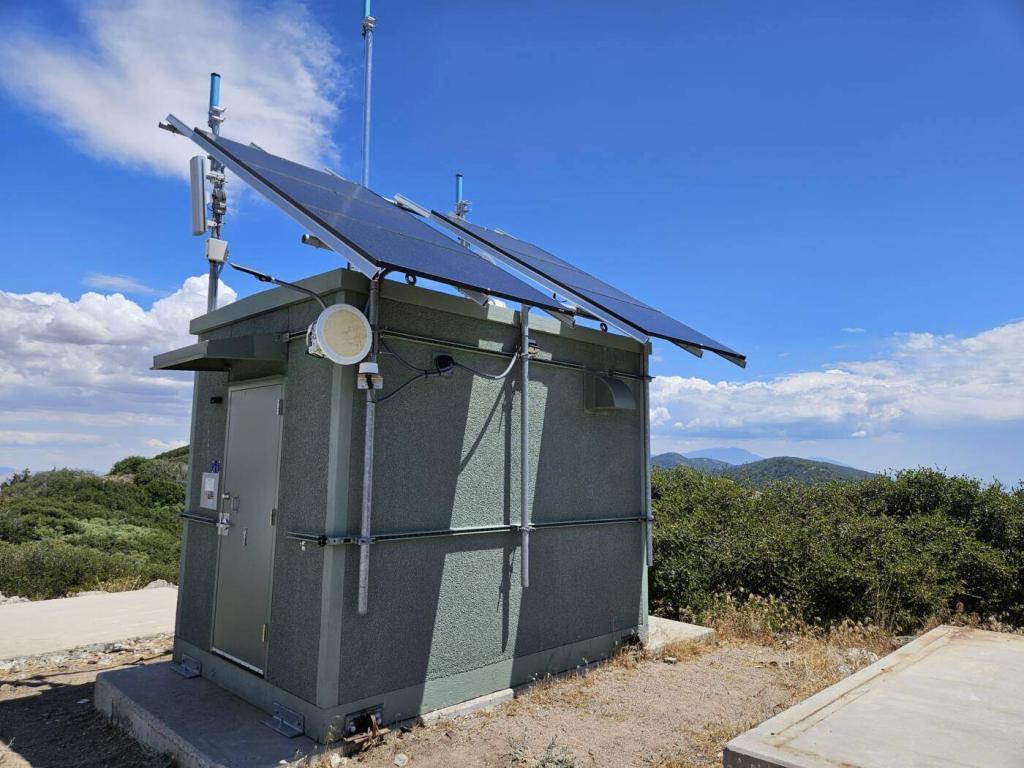
Being a mountainous area, the coverage is erratic as every one of the tower sites will cover only a portion of the pass so the radio has to constantly change tower sites depending upon where it is located within the pass. Each tower site change takes some time to acquire so the radios spend a considerable amount of time out of range looking for a tower site instead of being locked into a radio tower and ready to receive a call from dispatch. This meant that we needed to resolve the problem fairly quickly so that we could provide the expected performance within their coverage area.
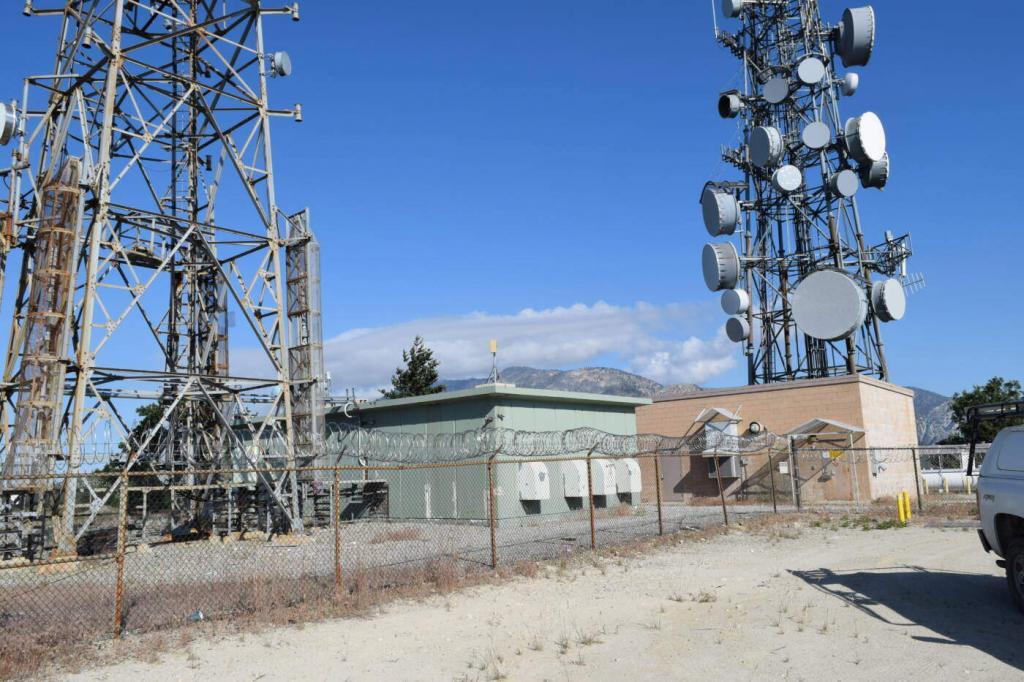
To meet the contract requirements, MRA embarked on a quest to obtain a tower site in the area. There were few developed tower sites that would cover the area. One was at the summit of the Cajon Pass which has cellular antennas and governmental radio systems at the site. Unfortunately, the site does not reliably cover the entire pass because of all of the twists and turns in the pass obscuring the line of sight from the summit where the radios are located. There is at least one cell site in the pass, but cellular companies generally will only lease space to another cellular company and will not allow a commercial radio operator to install equipment at any of their sites. The only tower site that we could identify that had fairly good coverage of the Cajon Pass was San Sevaine. This site was owned by American Tower, a large tower company that owns approximately 100,000 towers. They are very rigid in the way that they deal with customers and tend to be priced at the top end of the market. We knew that we would be required to pay a high price to be in their site but we felt that it was the only way to satisfy the FSP.
We contacted American Tower to see what it would take to place a radio at their site. They did not disappoint us. They wanted the first born, an arm and a leg. We spent a considerable amount of time negotiating with them to try to get an agreement palatable to us. We did manage to get some concessions, but in the end, the contract was heavily weighted in the favor of American Tower. We swallowed our pride and signed the agreement since they essentially had us “over a barrel” as the only tower owner who would rent us space to cover the Cajon Pass.
While we were negotiating with American Tower, we inquired with the US Forest Service about developing a new tower site at Cajon Mtn. Lookout. This was formerly a fire lookout used by the Forest Service in previous years, but was now abandoned as a fire lookout. The US Geological Survey had an installation at the site that measures the movement of the mountains and the US Forest Service had a small building that provided radio communications for themselves. There was no electrical power at the site and the Forest Service was not inclined to allow a power line to be installed at the site. Additionally, it could easily cost $1M to bring power to the site assuming that we could get permission to bring the power to the site. The radios from the US Forest Service were solar powered and so was the equipment from the US Geological Survey. Our equipment was capable of being solar powered, so we felt that would be the way to move forward with the Forest Service.
We made an official inquiry with the Forest Service regarding use of the site. Since it was not a developed site (the Forest Service uses sites for their purposes without the need of the scrutiny that is given to other entities, so we had to approach the issue as though we were petitioning the Forest Service to designate the site for electronic use without anyone else currently at the site.) This would require several steps including a biological study to determine the animal and plant life that would be affected by us being located there, archeological study to determine if there are any ancient Indian artifacts at the site, the development of a site use plan that would be used for MRA and any future user of the site to determine the rules and regulations that would control the use of the site and a California CEQA study to determine compliance with CEQA standards. This process could take years to complete with the current work load that the Forest Service had for their existing employees. Therefore, it was clear that we had to sign the agreement with American Tower to provide the service to FSP in a timely manner.
The paperwork that needed to be completed and submitted was considerable. To get this done, MRA uses an outside consultant who is tasked with obtaining entitlements and permits. The consultant set out to complete the paperwork as quickly as possible, but was often waiting for the Forest Service to be informed as to the next step or needed the Forest Service response before proceeding to finish. This meant that we were at the mercy of the US Forest Service schedule and their availability of personnel. We continued to push to get the site under review, but we were informed that it would be approximately 18 months before they would be able to review the package. They needed to write the management plan for future electronic use of the site which would take them about a year and then it needed to be adopted before they could review our submittal for the use of the site.
The management plan was sent to me for review. I read this massive document cover to cover since once it was adopted it would be the rules and regulations under which we would operate for the length of time that we occupy the site. Therefore, it was imperative that I have a full understanding of what it required of us to do. My review of the document revealed two items that of concern. I called the Forest Service representative to speak to her about the items, but the Forest Service was not inclined to change them since they felt that it was the correct way to manage the site. I raised my objections and put them on public record, but when they eventually adopted the management plan, it contained the terms to which I objected. I could have appealed the decision, but that would have considerably delayed the issuance of our permit (assuming that it will be issued) because they do not issue permits for the land use until the management plan is in place.
Now it was a waiting game for MRA. The firm that works on our entitlements had some issues with which to handle whenever the Forest Service stated that they needed some documents. These items included things such as a biological report on animal life or a botanical report on the plant life. We had to perform an investigation to determine if there were any ancient Indian artifacts in the area and we had to perform a radio interference analysis to determine if there was any chance of us interfering with the radios operated by the US Forest Service at the site. After another 6-9 months of processing, the Forest Service informed us that they would be issuing the permit for MRA to operate radios from the location. In all, they did not make it easy to get the permit to use the site.
After 3 years of work, we finally had our permit to use the site. That meant that we now had to implement the plan to construct at the site but we were in the middle of the COVID-19 shutdown which made everything to do with the project more difficult. Our original design called for using a pre-fabricated building manufactured by FiberBond Corporation, a large company that is well known for manufacturing buildings for telecommunications use. The existing concrete pad that we proposed to use had dimensions that we used with FiberBond to specify the size of the building. We ordered the building to be delivered to the site a long time before the permit was issued on the assumption that we would have the building ready for delivery as soon as we got the permit from the Forest Service, however due to the incessant delays with the Forest Service, we had to take delivery of the building at our office. This would cost us additional money to eventually transport the building to the site, but it would also make it easier for us to build out the interior of the building to make it ready for radios to be installed inside. It would also allow us to install strut on the outside of the building to facilitate the installation of the solar array and antenna structure. Therefore, we told the manufacturer to ship the building to our offices. The building arrived on the morning of January 15, 2021 at which time we had a crane pick up the building from the lowboy flatbed transport and set it in our parking lot.

During the time that we were impatiently waiting for the US Forest Service to clear the road to Cajon Mountain Lookout, we had the building in our parking lot which gave us the opportunity to perform a lot of the work on the building by walking outside instead of having to drive up to the mountain, a two hour drive each way to and from the site. I designed the interior layout of the building to handle the battery system and 6 racks to house the radio equipment to be installed at the site. The racks were installed per the layout design and the cable tray was installed to manage the cabling and provide for securing the top of the racks to make the entire installation rigid and as earthquake proof as possible. This is important because Cajon Mountain is a short distance from the San Andreas Earthquake Fault which if it moves can generate a massive earthquake. We feel that it is important to have the site fully operational in the case of a major earthquake as the MRA Diga-Talk network would be used by many people providing emergency assistance to people who have suffered damage or loss of loved ones in the event that we suffer from a major earthquake. Providing reliable communications that will survive natural disasters is of paramount importance and MRA strives to meet our responsibility to provide that level of service to our customers. This philosophy dictates what we do, how we do it and why we do what we do. It is our privilege and our duty to see to it that we live up to that philosophy.
In 2019, the permit to use the site was issued to MRA. However, we faced several problems implementing the plan to get the site up and operational. The first problem was that the road was in terrible shape thus making it impossible to transport the building to the site by truck. The brush had closed in on the road scraping both sides of the vehicle whenever driving up the road. There were many areas of the road that were far too rough to be able to transport a 35,000 lb building on the back of a flatbed truck. Additionally, the tilt of the road varied between being flat to almost 11 degrees tilt towards either side making it highly likely to have the truck and building end up on its side instead of completing the trek to the site. This required a major repair to the road which we attempted to get the US Forest Service to perform. They are responsible for the maintenance of their roads, but they continually cry poor mouth and claim that they do not have the money to fix the road these days. We spent 2 years trying to motivate the Forest Service to fix the road since they already had a radio building that they could not access except via helicopter. The US Geological Survey also had equipment at the site to measure the movement of the mountains. Neither organization seemed to be motivated to fix the road so after waiting enough time to be certain that neither of them were going to perform any road maintenance, MRA had to take the bull by the horns and clear the road. This was done in December of 2022 and the road was finally ready for us to move the building on December 16th.
The other problem associated with the delays in getting the site operational was COVID-19. Our company NEVER shut down a single day during the COVID-19 shutdown crisis. As a telecommunications carrier of essential services, we had to keep our services running during the shutdown and provide all the routine maintenance and emergency repairs that were required to keep our systems operating at peak efficiency. Many of our suppliers were shut down or suffered from supply chain issues which kept them from being able to deliver the items we needed in a timely fashion. Many of the items that we use had one year delivery cycles which can challenge any business. We had to anticipate many of our needs a year ahead of time. Some of the items that we needed for Cajon Mountain Lookout had extended delivery times that made it difficult for us to be able to obtain them in the normal time frame associated with procurement of these items. The result of this situation made us lose our incentive to get the job done quickly.
I had spent time looking at different methods of getting the building to the site. One idea was to have a sky crane helicopter take the building to the site. I made a considerable number of calls to find who does this type of work. The answer that I got ruled out this method of transporting the building to the site due to the maximum load that they could handle was 17,000 lbs and our building weighed twice that amount. In addition, their price was $150K and it would take at least 9 months before they would have time to handle our request. This ruled out this option and put us back to looking at ways to transport the building over land to the site. After calling and speaking to several companies who handle this type of difficult transport, we found a company that was willing to tackle the job provided we could get the road repaired to the point where they would consider it feasible to do the job so I contacted a firm that would perform the road work. They needed to see the road so that they could give us a bid on the job so on June 27, 2022, I went up to Cajon Mtn. to meet with Innovative Services, the company who was going to bid on clearing the road for us so that we could get the building to the site. They brought a 4WD quad off road vehicle which we used to traverse the road and get up to the site. The trip was quite an excursion because of the condition of the road and the amount of vegetation that was obstructing the road. At times there was a canopy of tree branches that were no higher than 4 feet off the ground which meant that we were being attacked by the branches as we drove up the road to the site. I took lots of pictures of the road during the trip which proved that I would not have been able to get my 4WD vehicle up the road in its current condition. My Tahoe was over 6 feet tall and there were so many areas of the roadbed that had issues, I would have gotten my vehicle stuck had I tried to get to the site. The trip revealed the difficulty of repairing the road and clearing the vegetation to make the road not only passable, but it had to be in exceptionally good shape so that the large vehicles that were needed to transport the building could get up the road in safety.
On December 5, 2022, Innovative Services began their road work clearing the brush and working on the road surface. Mark and I met the team at the road to make certain that everything would proceed properly and that they had access to everything that they needed. The gate to the site was locked and we had the key. We went up to the gate in our SUV which was difficult, but not impossible and proceeded to unlock the gate so that the road crew had access to the site. We then turned around and headed back down to where they were working at gave them the key to the gate in case someone came along and locked the gate. We took many still pictures and videos that day which we have in our library and some of them have been included in this story and are on our website. As they continued their work, we made another trip on December 9th to see the progress they were making. Weather was a concern because this appeared to be a winter with plenty of rain which was our enemy in relation to completing this project. After another week, we headed up on December 15th to see the progress on the road project and found the entire road covered in snow behind the gate. We drove up the road to the site to confirm access to the mountain and to prepare the concrete slab for receiving the building by cutting off all of the anchor bolts that were sticking out of the concrete that held the old lookout building that had been removed to the concrete foundation. These anchor bolts were in a place that interfered with our use of the site so we needed to saw them off. Additionally, we had to clear some of the brush which had grown up and spread onto portions of the slab. We wanted the entire concrete slab clear for bringing up the building and putting it in place.
It was now Friday, December 16th and the road was now ready for us to transport the building to the site. I called Pepe’s Tow who was going to transport the building to the site once we had the road ready for their trucks to haul the building and informed them that the road was scheduled to be finished by Innovative Services on December 16th. During the call, I urged them to come up with a date within the next few days to transport the building to the site. We decided on December 20th, the following Tuesday. The reason that I wanted this to get done so quickly is because I was concerned about the weather damaging the road to the point that we could not transport the building over the road. In fact, by Christmas Day, the road had been damaged to the point that we could not have gotten the building up the road, but fortunately on December 20th the day that we transported the building, the road was still in the same shape as 4 days earlier when it was finished being made ready for the job.

The 51 foot lowboy flatbed truck from Pepe’s Tow arrived at our office to transport the building to Cajon Mountain Lookout around 8:30AM. The rotator truck did not arrive until about 9:15AM which provided time for the level of anticipation to build up to the point where we were ready to explode with excitement. The rotator was set into position to pick up the building. The lowboy flatbed truck was then moved into position to receive the building. Since the rotator needed to use two lift cables which were attached to different portions of the building, it presented a problem of being able to get the building squarely on the back of the flatbed. This meant that the rotator had to be positioned just the correct way along with the flatbed so that when the building was lifted and swung around to the flatbed, the building was close to being perfectly square on the flatbed truck. This required quite a bit of planning especially since the size of our parking lot provided considerable restrictions as to how it would be possible to stage the vehicles. It took two different tries to get the building squarely on the back of the flatbed for transport to the site, but we finally had it done. Once it was in place, then the building had to be properly secured to the flatbed for transport which required a web of tie straps to be certain that the building remained in place during transport. While that was being done, the rotator truck had to pack up and get ready to leave which required retracting all the outriggers, stowing the pads that protect the parking lot, lowering the boom and securing it in place so that it does not move during the trip to the site. Now we were ready to leave the office and head to the site with the building in tow.
We had a full compliment of people to head to the site. There were two men from Pepe’s Tow, one driving each of the two trucks. There was myself driving my vehicle with Keith (our videographer) to record the event for posterity and Mark Lidikay, our drone operator who can get video from angles that can not be obtained by Keith on the ground. Additionally, I had my still camera in the car, my cell phone camera in my pocket where I keep it when not in use and Mark Lidikay had his high end still camera plus others who had their cell phone cameras. David and Chris were going in David’s pickup truck and we also had Fred and Mark who planned to meet us at the site. This meant that we would have 3 Marks at the site, a situation that could lead to confusion if we did not take the time to make certain that the correct Mark responded to orders that were being barked during the process.
We left the office around 11AM making our way to the freeway taking main streets so that we could properly transport the building and not run into difficulty with streets that were too small or had restrictions as to the size of vehicles and gross vehicle weight allowed. (Before leaving, we handed each of the rig operators a simplex radio so that we could all talk to each other in case something happened.) Our caravan entered the freeway on-ramp with David in the lead, then the rotator truck, the lowboy flatbed and finally my vehicle. We drove at 55 mph from the time we got onto the freeway until the time we exited the freeway except for the time that traffic would not allow us to drive full speed. We had at least an hour or more of driving to get to the off ramp at Hwy 138. Since it was now past 12PM, I let everyone know that I was going to stop at the McDonald’s near the freeway exit to pick up hamburgers for everyone. We were heading towards Silverwood Lake and then into the mountains where there would not be any opportunity to get anything to eat so I thought it would be prudent to make the detour while the rest of the crew continued heading towards the dirt road. After waiting in line for ordering and for getting the food for an extraordinary amount of time, we made haste to catch up to the other vehicles. Due to terrain irregularities, I was out of simplex range to speak to the truck operators, but I was able to speak to David who had his mobile radio set to listen to the MRA network which did have some coverage in the area. I drove at an excessive speed to catch up and eventually found them pulled over to the side of the road at Silverwood Lake. I did not know why they were stopped there, but I would soon find out once I pulled over and parked my Tahoe.

I parked my vehicle away from the two trucks that were parked side by side. They told me that they were going to transfer the building from the flatbed to another transport vehicle that was considerably shorter and had greater ground clearance. This made perfect sense to me because I had been concerned about the length of the lowboy trailer and how low to the ground it sat. They informed me that they had to use the flatbed to transport the building on the freeway, especially since we drove by a CHP inspection station just before getting off the freeway. However, for the rough drive up the mountain, they felt that another transport vehicle with good ground clearance and a considerably shorter wheelbase would make the transport up the hill far more practical. So we were all waiting along the side of the road for the new transport to arrive which gave me the opportunity to distribute the hamburgers to everyone for lunch while we were patiently waiting.

After about an hour of waiting, the new transport arrived. We had already removed all of the straps securing the building to the flatbed. As soon as the new transport arrived, they lifted the building off of the lowboy trailer and then the lowboy pulled out from underneath the building and had parked out of the way. Now it was time for the new transport to back into place so that the building could be lowered into place on its back and then secured with the tie downs. This included chain binders on all 4 corners of the building as well as other tie downs to make certain that the building did not move during transport. We were heading for a dirt road and although it was in particularly good condition at the moment, it is still a dirt road and not a paved road which is prepared to a higher level of professionalism meaning that it is smoother and more level than a dirt road. With 35,000 lb of building on its back, the transport had to be careful not to loose its load, especially in areas of the road where there is a side tilt to the road. With the building fully secure, it was time to resume our trek on the road after the lowboy flatbed took off to head back to the city after handing off the simplex radio to the new transport driver. We pulled out onto the highway and continued for a few minutes before we reached our exit at Cleghorn Road. Turning right at the bottom of the off-ramp, we drove for about one mile until we reached the end of the pavement turning into a dirt road. We stopped to organize our caravan. We took the lead with the flatbed transport in second position. The third vehicle was the rotator truck with David and Chris rounding up the rear in his pickup truck.
I started up the road at a slow speed. I wanted to stay far enough ahead of the flatbed truck to be able to warn them of upcoming obstacles and prevent kicking up sufficient dust to be a problem. (With the recent rains, dust was not a big issue, but could rear its ugly head under the right circumstances.) Something that would be almost meaningless to me could present a sizeable obstacle to the flatbed transporting our building so I would constantly be grabbing the microphone while barking out warnings about the road, rocks, narrow areas, sharp turns, dips or any other areas of concern to the transport. By leading the caravan, we did not have to be concerned that they might head the wrong direction and by trailing the pack, David could make certain that the rotator did not get lost or stuck behind. We slowly made our way up the road and when it seemed to be the right time, we lunged forward to get ahead so that we could let Keith out of the SUV so that he could get some video of the trucks heading up the road. After all the vehicles passed him, we stopped to let him get back into our vehicle so that he did not have to run to keep up with us the rest of the way up the mountain. (I don’t think that he could have kept up with us even though we were moving slowly.) We continued up the road getting past the private property turnoff, past two more switchbacks which had turns tight enough that the trucks may have needed to make a multi-point turn. Finally we reached the two cisterns that were built by the US Forest Service to fight fires in case of an emergency. However, this time of year, that was not a likely issue to encounter considering the recent rain that we have had in recent time. At this point, we were about half way up the dirt road to the site, but the more difficult section of the road still lay ahead of us to negotiate.
We were now approaching the switchback at the cisterns was wide enough to make the turn easy so we proceeded up the mountain after verifying that everyone was ready to proceed. We restarted the caravan while we took the lead again. We were now on the side of the canyon wall, slowly working our way uphill towards our final destination at Cajon Mtn. There are approximately 50 turns in the road from this point until we reach the gate that we need to unlock so that we can take the cutoff road to the site. Slowly we made progress towards the gate one turn at a time making sure that we did not get too close to the edge of the road where the ground could collapse under the weight of the truck. It was not just the weight of the building at 35,000 lbs, it also included the weight of the truck carrying the building plus the rotator crane a short distance behind the flatbed carrying our building. If the road gave way, the truck, the driver and our building would go tumbling down the canyon and the driver would likely be killed. Therefore, we were trying to make certain that everything that we did was done with safety in mind. The cost of cleanup, the human cost and the cost to the business if something went very wrong could be devastating so we felt that being cautions with our movements. We reached the gate to find that it was left open by the people who cleared the road, but the truck carrying the building needed to do a 5 point turn because there was a 180 degree turn in a fairly tight radius. Now we were in for the most difficult portion of the road which was cut into the side of the mountain. It was approximately 2,000-3,000 foot drop on the right side of the vehicle if the vehicle got too close to the edge of the road which could see the tire slip over the edge. There were many areas where we had a canopy of trees over our heads which were generally tall enough for us to pass, but there could be an exception so we had to keep up a vigilant eye on the many factors that could become a hazard which kept me busy barking out warnings about the different hazards that I would catch my eye.
There were approximately 60 turns between the gate and the site which meant that we had to stay vigilant dodging the turns, rocks and trees. We crept along the road at a slow pace especially in areas where the road narrowed leaving little room for error. Turn after turn presented challenges to the flatbed truck carrying the building with the overhead tree branches attacking the building from time to time. Eventually, we made it past the tree canopies and broke out into the open air with the sun shining down on us like a beacon from heaven. We finished the downhill grade from the gate and then started uphill for the final approach to the peak. Placing the SUV in first gear made the engine rev but gave us the required power to negotiate the final set of turns while dragging the load up to its final destination.
We arrived on top of the hill with the flatbed shortly behind us and the rotator truck closely behind the flatbed. I pulled past the location where the building was to be set to keep the area clear for the large trucks to be able to maneuver. Mark and Keith exited the vehicle and got set up for filming the operation of unloading the building from the flatbed transport and placing it on the concrete foundation. They set up their equipment and got ready to start the recording. Keith had his video camera with a stabilizer and Mark was flying the drone to get the aerial shots. In all, we were ready to document the process of getting our building in place.
Once the trucks were all up on top of the hill, the drivers got out of the truck cabs to assess the situation and determine how to stage their vehicles to make the unloading process as easy as possible. They then proceeded to move their respective vehicles into position. While this was proceeding, we got two visitors (Fred and Mark) up at the site to watch us unload the building and place it on the pad. (With only 10 people at the site, we now had 3 people with the name Mark.) The flatbed carrying the building drove up on top of the concrete pad where the building would ultimately be set while the rotator truck positioned itself next to the concrete pad while attempting to get the most optimum angle for lowering the building onto the concrete pad with the minimum strain on the rotator and the maximum angle advantage for the rotator to lower the building onto the concrete pad. The existing terrain at the site including the existing concrete pads created obstacles for the rotator to do its job and the flatbed to get into proper position but eventually they were both in the most advantageous position for their respective vehicles.

Now it was time to pick up the building, drive the flatbed transport truck out of the way and lower it into place on the concrete pad. With little fanfare, the building was lifted up into the air sufficiently high to clear the bed of the flatbed truck. The flatbed drove forward while each of the 3 rear axles dropped off of the concrete pad one at a time causing the flatbed to bounce up, but the transport did not hit the bottom of the building because the building was lifted high enough to account for the bouncing of the flatbed transport. Now the building was hovering over the top of the concrete pad so it was time to align the building to the pad and get it lower to the ground. The building was carefully lowered to within about six inches of the ground so that we could start the final approach to the final landing spot for the building. With the two lifting cables from the rotator truck each attached to different lifting hooks on the building, aligning the building was a challenge. Four of us tried to turn the building and hold it in place while the rotator attempted to set the building down the last few inches. We were able to get the building aligned with the pad, but we could not hold it while the building was lowered. There was just too much mass to the building for the four of us to handle.
Thinking about how to solve the problem, we tossed around several ideas and quickly settled on one idea that was simple. We had David move his pickup truck into position near the building and tied one corner of the building to his pickup truck with a tow strap. With the proper tension applied to the tow strap, we proceeded to lower the building to the concrete pad while the four of us applied pressure to the building to make the fine adjustments to get the building squarely aligned with the pad. Finally we had the building in place on the concrete pad foundation. It was time to release the tow strap that was holding the building into position, lower the lifting cables so that they can be detached from the building and pack up the rotator which was a similar process to what we had to do twice before earlier in the day while at our office before heading for the mountain and again on the side of the road when we moved the building from the lowboy trailer to the flatbed transport. It was time to pack up everything as quickly as possible because we were starting to lose the light due to the sun setting. With all the delays we had, it was fairly late in the day and since we were within one day of the winter solstice, the day was short with the light waning in the sky. It was clear to us that we would not get off the mountain before the light was gone. For David and me, it was not a big issue since we would frequently drive dirt roads in the dark, but the flatbed transport and the rotator truck were each a massive vehicle which makes it far more difficult for them to maneuver the road. They were not familiar with driving their vehicles under such conditions. Additionally, some of the road was still muddy which could cause the truck to slip while driving and with the great mass of their vehicles, once the truck would start to slip it may not be able to stop in time.

The building was finally in place on the mountain. The door was locked and building accessories along with some other equipment was placed inside for storage to be installed at a later date. Our priority was to get off the mountain, not to get the building operational. Mark and Fred took off in their vehicle while the rest of us continued to get ready to leave. There was a lot more work to be done up here on the building starting with bolting down the building to the concrete pad. The site is very close to the San Andreas Fault which if it moves would possibly shake the building off the concrete pad. Normally we would not be too concerned about a 35,000 lb building moving, but the power of an earthquake from a nearby fault could quickly ruin one’s day and prove that buildings can walk in spite of being an inanimate object. To prevent such an occurrence, it was prudent to bolt the building down to the concrete pad. We still had to build the solar structure, install the batteries, solar chargers, radio equipment, build the antenna structure, etc. Now was not the time to engage in such activity, but it was the time to leave.
We lined up the caravan in reverse order to when we drove up the hill. David took the lead and started down the hill. He was followed by the rotator, then by the flatbed and finally by myself. The light was quickly fading so we wanted to move quickly, but it was clear that the trucks could not move safely that fast and that we had to take our time moving slowly down the mountain and then back up as the road had to climb as it approached the gate. David proceeded through the gate followed by the rotator who had to make another 5 point turn along with the flatbed transport which also had to make a 5 point turn. We stopped to close and lock the gate then proceeded to drive down the road. It took us only a short time to catch up to the caravan since they move far more slowly than we were capable of driving. So now we were rounding up the rear of the caravan making sure that no one or nothing was left behind. Additionally, we were doing our best to be observant regarding anything that could interfere with the trucks safe journey down the mountain. Being completely dark at this time and being at the rear of the caravan which made it difficult to see anything at all, our ability to help was very limited.
We continued to work our way down the mountain slowly. There were several locations where there were puddles of water on the road which means that there would likely be mud under the water. This presents a challenge to many vehicles. The two large vehicles that we were escorting potentially could be more adversely affected than our vehicles. When we encountered one of these water puddles, the rotator crane truck started to slip which caused the truck to swipe the side of a tree near the edge of the road that bent the truck front bumper. It was not exactly clear what happened at the time or the extent of the damage to the vehicle but the damage was severe enough that we stopped the caravan while the driver inspected the front of his truck. In the dark, it was difficult to see the damage so we felt that we should continue down the road while taking extra caution when we encounter additional mud puddles.
We were now approaching the switchback where the cisterns were located which meant that we were now about 50% of the way down the hill. This U turn was wide enough that the trucks were able to negotiate the turn without having to back up to make a second attempt on the turn. We proceeded down the hill and within about 5-6 minutes, we reached the first of the five switchbacks that we would have to pass while traveling the bottom half of the road. This switchback was also a wide enough turn for the trucks to avoid a multi-point turn. This was another section with a sharp drop-off on the left side of the road so we had to keep from getting too close to the left hand edge. Now that we have negotiated the switchback, the drop-off was now on the right hand side of the road where we continued to head downhill heading towards the river crossing and then making a right turn to head east towards Hwy 138. We continued our slow trek towards civilization where we encountered another mud puddle but this time we warned the trucks and got them to slow down to a crawl so that they did not slip and slide. We entered an area where the road traveled over relatively level ground with a mild angle of declination which made travel on this section of road to be relatively safe. Another 7 minutes down the road was another switchback that was easily negotiated which lead to another switchback just 1-2 minutes later. We were now heading east again towards the highway along the riverbed which we could not see due to the darkness. If we stopped to listen, there were the sounds of crickets and other animals but we were too intent on getting off the mountain to take the time to enjoy nature and the outdoors. After another 5 minutes, we reached the 4th of 5 switchbacks and 1-2 minutes later we reached the last of the 5 switchbacks. We continued to head east paralleling the riverbed where we could hear the water running downhill. If I were a fisherman, I might be trying to get out my fishing gear, but I doubt that this river would have any fish since it does not flow year round. Another few minutes went by and we finally reached the beginning of the paved road. Here we pulled over so that we could get out the flashlights and inspect the rotator truck more closely. We found that the bumper was bent, but fortunately there did not appear to be any other damage to the vehicle. So now it was time to retrieve our simplex radios from the truck drivers and made certain that they were in good shape to head back to their base. David and Chris headed towards his domicile while I headed back to the shop to deliver Mark and Keith to their vehicles so that they could drive home.
It was a successful day. We were all tired and ready to head home. We each went to our respective homes and none of had any trouble getting to sleep that night.
Wednesday was a new day. The weather today was not conducive to working at the mountain and neither was the weather on Thursday. Friday we were taking off for a half day plus we were closed on December 26th and December 27th. By this time, we had massive rains and we did not think that it was possible to get to the site. When we eventually were able to attempt a drive up the mountain on January 18th, Mark and I drove up there to find a landslide across the road that made it impossible to reach the site. We found the landslide across the road about 1-2 minutes past the cisterns which are located about half way up the road to the site. I instructed Mark to get out the drone so that we could take some video of the road to help determine if the rest of the road was passable while I started hiking up the road to see the condition myself. The problem with the drone is that the road wraps around the side of the mountain which blocks the radio signal that controls the drone. If the drone looses signal, it returns to home, the point from which the drone was launched. One idea was to fly the drone at a higher altitude to maintain line of sight to the drone so that the radio control would continue to function. However, the drone is programmed to not exceed certain heights above ground and when the drone moves off the road slightly, it may exceed the maximum elevation because of the steep drop off on one side of the road which can cause the drone to suddenly and dramatically move out of range. We did our best to scout as much of the road as possible which indicated that the rest of the road was intact and passable, but since we could not scout the entire road, that was a supposition and not a hard fact. So after I finished my inspection of as much of the road that I felt comfortable walking, I turned around and headed back to the landslide. I had walked at least for 15 minutes which represented the majority of a mile. During that walk, I had spotted many areas where there were rocks on the road which would impede our use of the road, but not necessarily prevent us from driving through the area so I thought that it would be prudent to clear the road of as many of the rocks as reasonably possible during my walk back to the landslide. I cleared at least 200 rocks off the road making my way back to the landslide which made the road far more passable with far less effort. I could only hope that the rest of the road that we could not scout would be in similar condition or better.

We discussed the next step to getting up to the site. We talked about renting an earth mover to clear the road to the site. Our lease with the US Forest Service called for us to maintain the road to the site so we felt that clearing the landslide fit into that provision of our lease. We scheduled a trip the next day on January 19th to the site when the weather was clear enough for the four of us to attempt to clear the road. We located a small loader that we could rent from The Home Depot in San Bernardino near the bottom of the hill where the site is located so after completing the paperwork, we hooked up the trailer with the loader / backhoe and we proceeded up the mountain in the morning. The weather was fairly nice in San Bernardino but as we started up the mountain and eventually the dirt road, the temperature continued to drop. As we headed up the dirt road dragging the trailer with the loader / backhoe, we had to stop many times to perform some road maintenance because the road was bad enough that we did not think that we could get the trailer carrying the loader past the ruts, washouts and mud puddles that had overtaken the road.
We stopped about one third of the way up the road and got out the shovels. Water was running across the road which has eroded the road base and dug a channel in the dirt. We used the shovels to fill in the channel and make it smooth enough that the trailer would traverse the area. We continued up the road and soon found another area that needed some mitigation. Again we got out and used the shovels to mitigate the ruts in the road so that we could continue further up the road. This scenario repeated itself about 5 times during the next half hour which delayed our arrival at the staging area near the cisterns. There we got out of the vehicles and proceeded to unload the machine from the trailer. The temperature was around 45° which was cold enough that we would begin to shiver when we were standing around waiting for something being done by someone else to happen. As long as we kept busy doing something, we generated enough body heat to stay at a comfortable temperature. We proceeded to head up the hill with the loader and quickly found that placing a load on the engine would cause it to stall. Nick who was our experienced earth loader operator constantly needed to restart the machine over and over again when the engine had a load. This made everything take 2-4 times as long as what should have been necessary to complete the task.
We headed up the road approximately 0.2 mile to the landslide during which time that Nick had to restart the loader several times. Each time he placed a significant load on the engine, it stalled. He started to clear the road and the loader stalled on the first scoop of dirt that he was trying to move. Scoop after scoop of dirt was grabbed by the loader and almost every time, the engine stalled again but we continued to work away at the landslide in an attempt to clear it so that we could make it up to the site. Chris and I started working on the tree branch debris that was embedded in the mud in an attempt to make the job easier for the loader to help prevent some of the stalling that was constantly plaguing us during the work to remove the mud from the roadway while Nick continued to drive the loader clearing the mud. Mark was running the drone to create a video record of the work that we were performing so that we could share the experience with everyone. We worked for 2-3 hours digging one load of dirt at a time making a path which was still too narrow for our vehicle to pass so we had to widen the path before we had enough of the mud moved off the roadway to be able to drive the Tahoe through the landslide. We had at least 1-2” of extra space between the edge of the landslide and the sides of the SUV which meant that I had to drive carefully through the landslide to keep from leaving permanent markings on the side of the vehicle. Once we got through the landslide, Chris and I headed up to the top of the hill to determine if there were additional landslides or other obstacles that would prevent us from reaching the top of the hill while Nick and Mark continued to work on the landslide in an attempt to widen the path enough to make traversing the slide a more comfortable event.
We slowly worked our way up the hill following the winding road as we maneuvered our way around the rocks in the road. The slide was approximately 50% of the way up to the site, so we have another 3.6 miles to go once we passed the slide. Overall, the road was in reasonable condition compared to a road that was impassible, but was a bit of an obstacle course compared to a normal road. We had to swerve left then right then left again to dance around the rocks on the road. There were broken tree limbs deposited onto the roadway which had to be cleared along with more rocks. We managed to get to the gate to the site so now we had to use the key to get the gate open. The gate mechanism was not very cooperative with us since the gate post that was used to lock the gate closed had shifted making it very difficult to remove the locking pin after removing the padlock which was very difficult to operate.
Continuing up the road to the site, the roadway was passable but with many obstacles. There were mud puddles, rock slides and tree branches on the road. We found the path of least resistance as we wiggled our way up the hill while avoiding the inevitable rock finding its way to dent, clang and puncture some necessary part of the vehicle undercarriage. The SUV does have skid plates installed in certain areas in the undercarriage of the SUV, but many areas are still exposed and susceptible to rock damage. Additionally, the large number of rocks on the roadbed represented a considerable risk that a sharp rock would pierce the sidewall of the tire causing a flat tire and a non-repairable puncture. It took time to avoid what seemed to be the inevitable outcome of the trip, but we eventually arrived at the site where the temperature was even lower than the 45° we experienced down at the landslide.
Upon arrival at the site, we used the key to open the building to see if there were any water leaks inside the building and determine if everything seemed to be OK. After walking around the building and snapping a few pictures, we got back into the SUV and proceeded down the hill.
Unlike our trip up the hill where our goal was just to make it to the site, this time we were stopping at many of the rock slides to kick and throw rocks off the road so that the drive would be far less hazardous. There were times when Chris was out there by himself clearing rocks and other times I was out there with Chris clearing rocks. We worked diligently clearing the road so that the trip up the mountain to perform the work would go smoothly without losing any tires or significant time getting to or from the site. We took at least another 45 minutes clearing debris to make the road far easier to navigate as we drove down the road towards the gate. We closed and locked the gate behind us as we continued down the road heading back to the landslide area. Nick and Mark had wrapped up their work on the road and were driving the earth loader down to the trailer which was parked down near the concrete cisterns so it was upon us to make better time heading down the hill. Therefore, for that reason and the fact that we were now on a public road instead of a private road behind the gate, we were not going to stop to clear the road except for areas where the rocks were particularly difficult and dangerous. We found 2-3 of those areas on the main road where we stopped to clear some rocks, but we did not do as thorough of a job due to time constraints. Eventually, we passed through the landslide and then we made it back down to the cisterns where we met up with Mark and Nick. We asked them why they had not cleared more of the landslide and they responded that they went as far as they felt that the machine would allow them without severe difficulty so they wrapped up their work and took the machine down to the trailer to load it onto the trailer while they still were able to get the Kubota to move on its own. Loading the earth loader onto the trailer by hand would have been an impossible task.
At this point we wanted to complete our trip down the mountain to the freeway so we headed down the hill without stopping for any more rock clearance, but we had to proceed slowly to avoid having an unfortunate situation occur with the trailer holding the Kubota loader. We had to traverse the locations where we performed road maintenance to make it passable for the trailer with the Kubota loader. These locations presented several challenges because we did just enough work to be able to get past the area without losing the trailer, tires or the machinery which means that the road was very rough and difficult to pass. However, after taking our time and driving carefully, we managed to make it completely down the dirt road to the pavement where we stopped to make certain that everything was secure before continuing back towards the freeway.
We thought that things would be clear sailing from now on, but we were severely disappointed. When we were approximately a quarter mile from the freeway on Hwy 138, everything came to a complete stop. Traffic was completely snarled and moving at geological speeds which meant that we could have gotten out of our vehicles and walked faster than we were able to drive in the vehicles. Traffic would intermittently move 5-15’ at a time making progress painstakingly slow. We got out our traffic map apps to see what was happening and to see if there was any way around the problem but there was no effective way around the problem that was caused by an overturned truck on the freeway blocking the Cajon Pass. It took us 2 hours to get down to San Bernardino from this point which is supposed to be a 10 minute drive to return the earth loader and trailer to where we rented the machine.
To return the machine, we had to take it to a manual car wash first. They charge a cleaning fee of $200-$400 if the machine is returned dirty depending upon how much work it takes to clean the machine. So while Mark and Nick were taking care of getting the machine cleaned, Chris and I went to the rental yard to discuss the problem we encountered with management to see what compensation they would offer us for the problems that we had with the earth loader. They did offer us 50% of our rental fee back. The manager we spoke to said that his offer was the best that he had the authority to offer and that if we wanted a larger refund, it would have to go higher up the organization. We reluctantly accepted his offer because we felt that it was more hassle to try to get a larger refund than it was worth. The machine did accomplish the task in spite of the trouble that we were having with it so the refund that they offered was reasonable under the circumstances. However, this brought up the point that we might have to go back to finish the job and have to rent the earth loader again which would cost us more than the 50% refund we received if we felt it necessary to go back to complete the job. It was now 6:45PM when Mark and Nick arrived with the cleaned Kubota and trailer. We completed the paperwork and started on the road heading home by getting on the westbound 210 freeway in San Bernardino. I suggested to the guys that we stop to have dinner on the way home and everyone was in favor of the idea. We stopped at Pinnacle Peak in San Dimas to an exceptional meal then headed towards home. In spite of all of the problems, we had a successful day because we now had access to the site to continue our work of getting the site online.

The next week on Tuesday, January 24th we made our way up the mountain to start making the site ready to be occupied by our radios. We started with hauling some of the 65 batteries to the site in our vehicles, bolted down the building to the concrete slab and started erecting the solar panel pipe frame to support the solar panels. Each battery weighs about 80 lbs so there was far too many of them to transport at one time so each trip to the site brought another batch of batteries up the mountain and then placed into the battery rack. We have two separate solar systems in the building including the 12 volt system to run our radio equipment and 48V to run the microwave system that will be used to connect the site to our network. We went back the next day to continue working on the building to bring another load of batteries, connecting the batteries with the proper jumper cables, continue working on the solar array and install a new deadbolt lock into the building door.


The winter continued with its fury by throwing storm after storm at the State of California which desperately needed the water that was supplied as a result of the storms. Unfortunately for MRA, it made our life difficult trying to keep our network fully operational and made it even more difficult to access the tower sites which included Cajon Mtn. Lkt. Eventually on April 18th, we were able to schedule a trip up the mountain to see what condition existed on the road to the site. Mark and I left the office to head to Cajon Mtn. with the idea of doing a reconnaissance mission to determine if it was possible to get to the site and clear any obstacles that might be in the way of us returning to the site to continue our work of getting the site online
. We started driving up the dirt road and found many obstacles which were impeding our progress, but not preventing our ability to get to the site. We cleared many of these obstacles on the way up the road, but left far more of them because we did not know what additional obstacles we would encounter and we wanted to have sufficient time to deal with whatever we would encounter. Eventually, we made it to the locked gate which we opened and proceeded through. The road had definitely taken many hits to easy travel on the it with lots of rocks down on the road surface, but when we arrived at the tree branch that had broken off the tree and slid down the hill blocking about 90% of the width of the road, it was time to stop, get out of the car, grab some tools and start cutting away at the tree branch so that the road would be passable.
There was snow packed below the tree branch which was shading the sun from melting away the snow so I got out the shovel and started shoveling snow after I broke the only saw blade that I had for my electric saw that I was using to cut away at the tree branch. Mark kept working on the tree branch while I started clearing more rocks from the road and eventually we had the road cleared to the point where we felt comfortable continuing up the road to the site. We stopped and cleared the really large rocks, but left all the medium and small size rocks that we felt should be cleared to get to the site and verify that the road was passable all the way to the top of the mountain. Eventually we made it to the site where we declared victory, opened the building to verify the integrity of the site and take some pictures. We stayed only about 5 minutes, but that was all we needed because the goal was to verify our ability to reach the site with a work crew and not to perform any work at the site.

With other work that we had and the fact that the weather continued to be challenging in terms of wind, we delayed heading back up the mountain because we needed to get the solar panels mounted on the mounting grid. The solar panels were 1 x 2 meters each which made it handle like a sail except that it was rigid and not flexible. The winds in the Cajon pass area were continuously high enough to make it unlikely to be able to deploy the panels. So we waited impatiently until May 30th when we scheduled another trip up the mountain to bring more batteries and install more battery jumpers. The winds were high enough to continue to prevent us from installing the solar panels. Other work was performed at the site working on lighting and ventilation for the building. However, on June 14th, we returned to the site with the final set of batteries and deployed the solar panels and built the bracing to keep the batteries from being thrown out of the rack in case of a major earthquake. Since the site resides a few miles from the San Andreas earthquake fault, bracing the batteries was a necessary step to preventing a disaster in case of a major earthquake. We also started installing the radio equipment by bringing up the repeaters and transmit combiners. I had to take some receive filters that we had at the shop to tune them to the correct frequency range and then to figure out the phasing harness cable lengths to make both sets of filters to be fed with a single antenna and have a single output to feed the master receive distribution system which feeds the receiver signal to all of the receivers at the site.

I challenged the guys to get the site finished and online prior to July 4th but to no avail. The solar chargers were giving us trouble and we had to replace the 12 volt charge controller which we had to order and wait for delivery after July 4th. So on Friday, July 7th, we went to the site and installed the new solar controller to get the entire 12 volt solar power system functional. We then installed the new transmitter jumper cables that were sufficiently long enough to connect all the transmitters to the transmit combiners without having to stretch the cables so that the wiring would be clean and neatly dressed. We also had the alarm company up to the site to install the burglar alarm wiring the alarm to work from our 12 volt power system and report the alarms wirelessly since there are no telephone lines to the site. So now we were able to power up the radio equipment and verify that we had a working site. We were having some difficulty with the temporary cellular data modem which we were using to connect the site while we were working on installing the permanent microwave link to bring the network connection to the site. The cellular modem was giving data errors and then would clear up when we rebooted the modem. Unfortunately, an hour later we had to repeat the process and then again. Finally, we replaced the cellular modem and got the connection to be stable. So now we had a working site, but we still have not installed the radio antennas so the coverage from the site was about 100-200 feet from the site. I worked on getting the updated programming into my radio and a radio from the alarm company that uses our network and finally ran out of things to do at the site.

Now it was time to head down the road back to the office while clearing more rocks off the road to make the road friendly to motor vehicles. I started down the hill with one of the alarm company vehicles 1-2 minutes behind me. I stopped about 10 different times to clear rocks and other debris off the road and each time the alarm company vehicle caught up to me before I finished clearing the rocks from the road. There were places that had rocks that I did not clear that had fewer rocks or smaller rocks as I concentrated on areas that had a larger quantity of rocks and larger sized rocks. I also cleared a few small tree branches from the road thus making the drive along the road to be easier. Eventually, I made it to the gate where I cleared more rocks. After passing through the gate, Fred (from the alarm company) closed the gate while I was heading down the road at a faster clip than Fred who does not drive the mountain roads very often, but that gave me time to work on clearing more rocks without holding him up very much or very often. There were 3 spots where I cleared rocks outside the gate which was consistent with my policy of paying more attention to the areas behind the gate than the public area outside of the gate. Eventually, we made it down the hill where I stopped to chat with Fred, straighten out the items that were thrown out of position while traveling on the road, picking up my trash that blew out of the vehicle when I opened up the door and taking a few pictures before continuing down the hill to the freeway and back to the office without any problems or fanfare.